成果を出す倉庫作業改善のポイント
国内のトラック不足は更に深刻さを増しています。この状況は東京オリンピック開催の2020年をピークに、その後も大幅な解消は見込めないと考えます。その第一の要因はドライバー不足であり、物流業界における積年の課題が顕在化した結果とみるべきでしょう。
物流業界の課題はトラックドライバー不足に限ったものではありません。倉庫作業の労働力不足も顕著に現れており、その影響は今後大きな問題として物流業界に圧迫するでしょう。そのような環境の中、「物流コストアップの抑制」という切り口でみると、他社リソースに頼らざるを得ない「トラック運賃」が上昇傾向にある中、自社努力で効率向上を実行できるのが「倉庫作業コスト」の領域です。
作業員の募集が困難な中、労働力を保持するために人材派遣が多用され、通常の作業員(直接雇用のパート、アルバイト等)の時給と比較して20%近くコストが上昇します。現場作業員の時給上昇は荷主企業の物流コストを上昇させ、物流企業の収益を悪化させます。運賃上昇がそうであったように、物流企業が荷主企業へ作業費の値上げを要請するタイミングはもう間近です。今回はこれからの労働力不足時代にこそ取り組まなければならない「倉庫作業改善」に注目し、確実に改善効果を出すための視点と活動ポイントを提言します。
目次
変化する物流コスト事情
運賃の上昇
2014年からの運賃トレンドは、留まることなく上昇傾向にあります。ドライバーを就職先として選択する人材が不足しているため、配送できるトラック数が減少しています。
結果として運賃上昇を引き起こし、解消される見込みが立ちません。ドライバー職が不人気な理由は①給与水準が低い②ドライバーになるための障壁(免許が必要)がある③労働時間が不規則である④3K職場(きつい・きたない・危険)であること⑤長距離ドライバーは家に帰れない。などがその理由として挙げられます。
この環境が改善され、他の職業と比較して魅力あるものにならなければ、稼動できるトラック台数(ドライバー従事者)が増加することはなく、ひいては運賃上昇トレンドが収まることが困難になります。
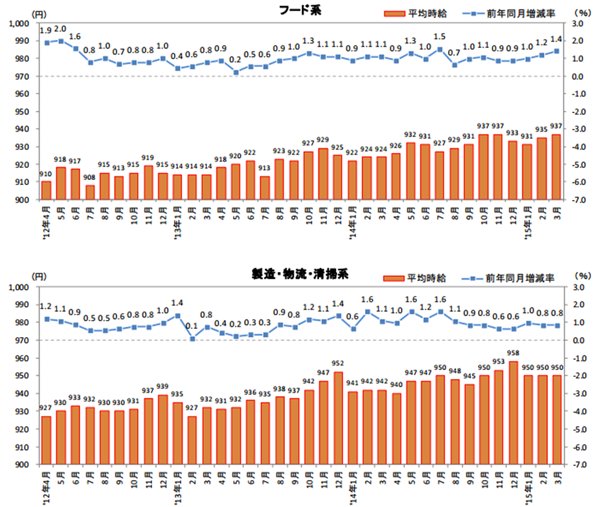
倉庫作業員時給の上昇
右の図は『三大都市圏(首都圏・東海・関西)の製造・物流・清掃系 平均時給推移 直近36か月の動向』(出所:リクルートジョブズ)で製造業物流・清掃業の作業人件費の変化を表しています。2011年5月度から景気上昇に合わせ店舗販売などその他業界の採用も活発になると、労働環境や作業負荷などからみて、物流業界への就労が敬遠されることになります。
物流現場では求人を出しても応募者が集まらず、パート時給を上げることでなんとか集めようとします。しかし、新しく採用するパート作業員が高い時給で、既存の作業員が時給据え置きというわけにもいかないため、既存作業員の時給はそのままで、あとは人材派遣でしのいでいるのが現状です。一層のコストアップを招く悪循環になっています。
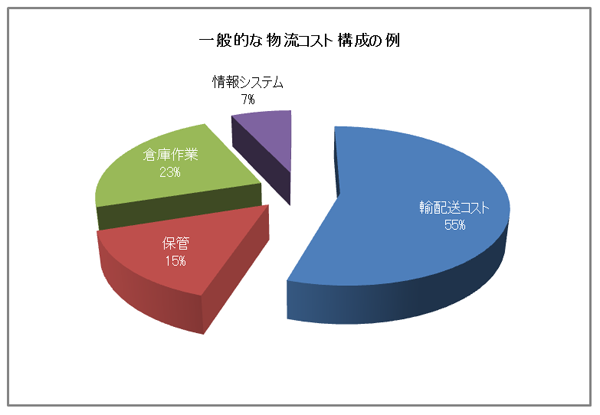
上記に挙げた「1.運賃の上昇」「2.倉庫作業員時給の上昇」は企業の物流コストを大きく上昇させます。国内企業の傾向をみると「①運賃」と「②倉庫作業コスト」でトータル物流コストの約60%~80%を占めます。もちろん企業によって多少のコスト構造は異なりますが、物流コストの大半が上昇基調にあることは間違いないのです。
そのような中で今後の物流コスト上昇の抑制、あるいはコスト削減策の一手として最も効果が期待できる取り組みが「倉庫作業改善」です。人件費上昇はもとより労働力の確保が困難な時期だからこそ倉庫作業に注目するべきなのです。
倉庫作業の状況と問題点
倉庫作業改善に取り組むにあたり、まずは倉庫作業で必ず発生する現象と問題点を確認します。
ケース1:人をまとめて投入して短時間で処理している(倉庫内に人が集中している)
現象
倉庫内の作業工程ごとに作業員を集中させることでまとめて作業する。一つ一つの工程を順番に完了させながら次の工程に進む(=渡り鳥作業)。
全体で活用できる時間を考慮せず、とりあえずできる限り人の手で作業を進め、順番に次工程に広げていく人海戦術方式です。
問題点
仕事量が多いからといって工程に人をまとめて投入すると、忙しく人が「動き」回るため業務が進んでいるように錯覚するかもしれません。しかし実際はムダの塊になっているのです。
問題①ムダな「動き」が発生する
人が集まって作業することで、ひとりひとりの作業スペースが考えられた物の配置でなくなります。限られたスペースで作業することで、物を動かすのでなく、人が動くことになります。その結果、移動のムダ、置き直しのムダ、動作のムダが発生することになります。
問題②異常がわからなくなる
人が集まって作業すると、思い思いのモノの配置や作業手順で作業をすることになり、作業基準が守られなくなります。その結果、基準時間などが守られず作業者それぞれのやり方でそれぞれのペースで作業することになり、異常がわからなくなります。
問題③スペースが広がる
人が集中するということはそのためのスペースが必要になります。立つスペース、作業テーブルのスペース、物を置くスペースをまとまって確保することになります。
ケース2:工程別に人とスペースを分割している
現象
作業工程を区分し、工程ごとに人員とスペースを確保している。モノを移動することによって工程間をつないでいる。(=分断作業)
初めに組み立てた現場工程がそのまま残ったことで工程間を繋ぐ動きが残っている。
問題点
問題①タッチ回数が多くなる
作業が分断されていると工程間で物の受け渡しが発生します。物の移動、受け渡しは付加価値を生む動作ではなく、単なる無駄な動きといえます。
問題②手待ち、滞留の発生
工程が分かれるとそれぞれの工程によって作業スピード差が生じます。後工程が前工程より作業が早い場合、後工程に手待ち時間が発生することになります。またその反対に前工程が後工程より作業が早い場合、後工程との間に滞留が発生することになります。
問題③広いスペースが必要になる。
工程が分かれることで、それぞれの工程の作業スペースが必要になります。工程が分割されるにつれて、作業自体のスペースと合わせて物を受け渡すための滞留させるスペースを確保することになります。
問題④動線がのびる、歩行が増える
工程が分かれることで工程間を繋ぐための歩行が増え、作業スペースが広がることで細かな歩行も増えることになります。
ケース3:倉庫に仕掛り品が滞留している
現象
倉庫に物があふれている。その理由も在庫過多や保管スペースの不足ではなく、作業スペースの周辺および通路に物が滞留している。物が置かれている場所も所定の決められた場所ではなく、通路をはじめとした空きスペースに物を仮置きしてまかなっている。
問題点
問題①滞留品によって現場の異常が見えなくなる
滞留品によって現場の正常が見えなくなります。必要な量が次工程に順次流れる現場は物が滞留すると異常発生がすぐに確認できます。一方、慢性的な滞留が発生している現場では異常ばかりが目に付き、何が正常かわからなくなります。生産性は悪いのはわかっているが、何から手をつけたらよいかわからないといった現場の多くがこれにあたります。
問題②滞留品によって無駄な動作が生まれる
滞留品は倉庫の中にスペースを必要とします。それによって余計な歩行や物の移動が発生し、基準外の時間が必要になります。
ケース4:作業進捗は経験測を元に感覚でコントロールしている(作業者任せ)
現象
現場の基準値及び作業進度に明確な基準を設定しておらず、現場担当者の感覚でコントロールしている。特に熟練者の多い現場ではよくみられる光景です。熟練者の頭の中で仕事量と終了時間が組み立てられている。仕事量の増減に関係なく概ね同じ時間で作業終了する現場です。
問題点
問題①作業員任せで現場が動いている
倉庫作業現場で基準とルールが明確に決まっていない現場は、作業員の采配や作業スピードに任せることになります。その結果、作業者にコントロールされた現場ができあがってしまうのです。作業量に関係なくいつも同じような時間に業務完了している様な現場はまさにこの状態といえます。
問題②異常が把握できない、改善できない
作業ルールや進捗管理が視えないと現場の異常が見えません。異常が見えない現場では何が異常で何が正常なのかの判断がつかないため改善の焦点も合わず、着手できないままになります。何かおかしいが何をしたらよいのかわからない状態が続くのです。
ケース5:改善活動が継続しない
現象
一度は「勢い」で改善された現場も、それ以降の変化が無くなります。または一度施した改善も以前の作業方法がやり易い、早いと判断されて元の作業方法に戻してしまうことが多々あります。現場は変化を嫌い、管理者も現場の現状を数値で把握できず、問題まで把握できていないため改善策が出てこない。
問題点
問題点①改善を検証できない
もともとの現場の問題点、改善の目的、目指すべき効果を理解せずに改善に取り組んだ結果、その取り組み効果を定量的に検証できず、慣れから判断して現場を元の状態に戻してしまう。
問題点②改善の必要性を感じていない
現場作業員が現場改善の必要性を感じていない。自分たちの仕事場(=倉庫作業)を維持するためには現場改善が必須であることが認識されていない。
結果・提言:効果を出す倉庫作業改善の取り組み
前述のような現場は非常に多く見かけられます。なぜそのようなケースが多くみられ、そのままの状態で残されているのでしょうか。それは「それでも現場は回る」という見方と「一度回り始めた現場は現場任せでも完了する」という現実があるためです。
しかし、今ができているからこれからも問題ないという考え方ではこれからの人件費上昇と人材不足をクリアすることは不可能です。人件費の上昇以上に作業能率を向上させなければ収益の好転は見込めないことは誰が見ても明らかです。そのために実行することは単純です。作業改善による作業能率の向上しかありません。
作業改善はただ闇雲に取り組むのではなく、手順・視点にコツがあります。その中でも効果の高い取り組みの視点は下記になります。
1.作業に流れを作る:団子作業をやめてひとつずつ流す
作業を組み立てるとどうしても分割して各々に人や場所を配置・確保しようと考えがちです。そのような体制の中で作業時間に制約がつき始めると、短時間でそれぞれの工程を処理しなければならないことになります。短時間に作業を処理するためにできる限り多くの人員を入れて取り掛かることになります。
まとめ作業は物を溜めてまとめて作業することになるため、置き場所と人員が必要になります。場所が広がり、人が集中するとムダな動作が必要になります。
まずやるべきは、業務を一つ一つ流すことで流れを作ることです。
そうすることで各工程の業務は、一つ完了したら次工程に流すことになり、手の届く範囲で業務を完了することが可能になります。また、一つ一つ完了させることで作業員一人ひとりに一定の業務スピードが作られることになります。
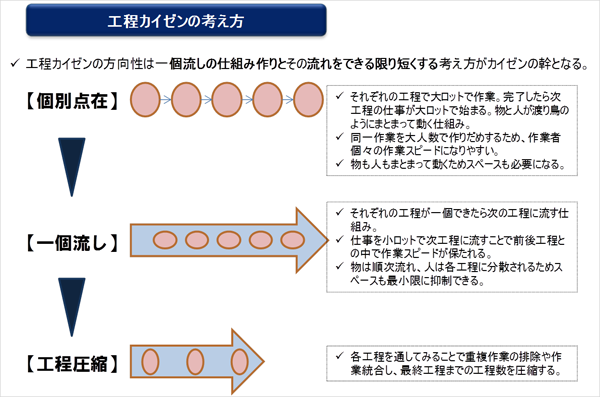
2.分断された作業をつなげる
工程が分割されると、工程と工程の間をつなぐためのバトンタッチが生まれます。文字通りタッチ回数が増え、そのためのムダな動きが発生することになります。
①工程間をつなぐための商品出し入れ:前工程から後工程に物を移動させるための時間、歩行が発生する。
②スペースの分割:工程が分割されるということはスペースも分割されることになります。分割すればするほど、作業を完了した工程のスペースは稼働率が低下することになります。
3.前後工程の作業スピードを合わせる
前後工程のスピードが合わないことで2つのムダが発生します。
①手待ちのムダ:前工程が後工程より遅いと、後工程に手待ちのムダが発生することになります。
②滞留のムダ:前工程が後工程より早いと、後工程に物が滞留することになります。
前後の工程スピードを合わせるには下記の方法があります。
①1つ作業するスピード差にあわせて工程に投入する人員を調整する。
②工程間に標準手持ち量(工程間バッファ)を設定し、工程間滞留が一定量溜まった時点で早い工程が遅い工程の応援に入って調整する。
4.管理者の決めた作業スピードで予実管理する
現場作業者に作業スピードを委ねると、業務終了時間を意識したスピードになります。作業量が増加しても毎日同様の時間に終了するような事態は発生していないでしょうか?
このような作業員任せの作業スピードから「管理者主導の作業スピード」に移行するには「管理者の決めた作業ルール、許容ライン」を現場に提示することが必要です。下記はその例です。
①工程別の作業基準時間 | (例)検品 30秒/件 |
②定位置 | (例)入荷品置き場の線、保管置き場の線 (例)棚の上の置き場表示 |
③作業手順 | (例)検品作業手順書 |
④作業終了時間 | (例)作業進度管理板(時間毎の作業量掲示) (例)目標終了時間 |
⑤標準手持ちの設定数 | (例)検品工程:標準手持ち10個まで |
現場の管理者はこのような指標を現場に視える形で表すことで、現場作業員は基準を意識した作業が実行できるようになります。
5.異常を管理する(5S・監督者の基準作り)
改善を継続するには常に問題点を見出さなくてはなりません。しかし「問題点」とは何でしょうか?問題とは=「基準から外れるものです」。つまり問題点を顕在化しようとするのであれば現場に基準を明確にし、それから外れる事象=異常=問題点なのです。前述したような管理者の考える現場基準をルールとして現場に浸透すること=異常が視える現場になります。異常が視えるとそれが改善対象となり、その真因を追究することで改善活動が進みます。すなわち基準、標準を作れば改善は見えてくるのです。
最後に
今回は倉庫作業改善の視点をお伝えしました。しかし、改善実行とPDCAを定着させることは容易ではありません。物流現場は変化を嫌い、新しい業務手順と今を比較して「感覚的」に今が一番良いと選択する傾向があるからです。
そのような倉庫作業改善を成功、定着させるには3つの大事なポイントがあります。
1つ目は現場に改善の必要性を理解してもらうこと(客観的な現場評価と改善に対する意識改革)です。改善はその必要性が認識されなければ実行、検証、定着まで及びません。そのためには現場が必要性を理解したうえで改善に臨む必要があります。
2つ目は早い段階で成功を体験することです。改善は手間もかかりますし、地味な活動です。自らの活動が具体的な成果(数値)として確認できることで、取り組み姿勢は大きく変わります。
3つ目は現場の活動を評価する場を持つことです。改善に取り組まなくても問題なく回る現場では、何の後押しもなければ誰も率先して改善に取り組まなくなります。改善活動の必要性を会社が啓蒙し、活動に対して会社の評価を伝えることが改善継続の土壌を培うことにつながります。
改善活動は現場だけのものではなく、企業の考え方そのものといえます。人財確保が困難な時期だからこそ、生産性とそれを支える考え方を再構築することが、他社に負けない競争力(現場力)になるのではないでしょうか。