これからの物流コストダウン手法について ~如何に効率を高めてゆくべきか?~
〔PR〕サービス/物流コスト削減
過去の物流コストダウンの背景について
物流コストダウンは、初期的に物流専業者へのアウトソーシングによって推進されてきた。一般的なアウトソーシングによるコストダウンは、その専門性を活かした業務効率化によるものが主である。しかし物流に関しては、それ以上に下記2つの理由に依るところが大きい。
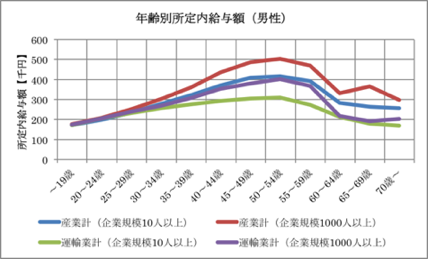
(厚生労働省:賃金構造基本統計調査より)
ひとつめは「物流企業の人件費単価が安いこと」である。人件費単価の相場については図1に示す通り、産業計に対して運輸業計は20%程度低い。物流会社にアウトソーシングすることで、作業人員数は変わらずとも人件費ベースでコスト圧縮が可能となることがお分かりいただけると思う。
ふたつめに「物流マーケットにおける差別化要素の少なさによるディスカウント体質」がある。物流業界は典型的な受注産業であり、荷主企業の成長=物流企業の成長という前提と、自社オンリーワンの差別化されたサービスを作りづらいという二つの前提がある。荷主企業の要望に応えることが取引継続の手段である物流企業にとって、その要望がコストダウンであれば応えざるを得ず、放置すれば他の物流企業がコストダウンを提案し、相見積やコンペになれば自社の利益を削ってでも取引継続を望んできた、いわゆる受容の結果なのである。
荷主企業側も同様に、際立った業務改善なくして単価ダウンを優先してきたことが、物流マーケットのディスカウント体質を助長した事実は否めない。このような背景から物流コストダウンは、改善より物流会社の特性(人件費単価の低さ)と物流会社の利益を削る形(物流会社による局所的な改善)で進んできたといえる。
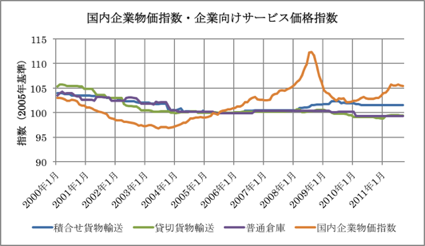
(日銀:企業物価指数、企業向けサービス価格指数より)
図2に物流に関する企業向けサービス価格指数を挙げているが、2004年までは上記のような手法でのいわゆる単価ダウンが可能であったが、それ以降は単価が下げ止まっていることが伺える。実際のコンサルティング現場での感覚は、今でも案件によっては単価ダウンが可能な場合も見られるが、その割合は年々低下していると感じられる。
今後は単価ダウン手法から抜本的な物流改善手法に切り替えられない企業は、コストダウンの実現が困難となることを十分に認識しておきたい。
取り組むべき改善について
物流改善の成否を決めるのは、拠点配置であると言っても過言ではない。もちろん拠点からだけでなく、輸送・作業・保管の個別の観点から導きだした最適な拠点政策を取らなければならない。輸送・作業・保管についての視点は次のようになるかと思う。
(1)輸送の改善
輸送に関しては販売物流および調達物流の複眼観点から判断することが望ましいが、調達物流を仕入先に依存している場合は、販売物流を優先して検討すべきであろう。
その際の重要なポイントは、センター納品等の「大ロット輸送」および「特定エリア共配」の実現である。
大ロット輸送については輸送距離が短くなることで車両トン数の選択自由度が増し、積載率を高めた輸送が可能となる。輸送距離の短縮が困難な場合は、共配の仕組みも合わせて検討すべきである。
また、特定エリア共配については、都市部を中心に従来路線便・宅配便にて出荷していた部分を地場(地域)運送会社が構築した面配送ネットワークにのせることを考える(現在、この仕組みの構築が最も即効的かつ大幅なコスト削減を実現している)。この場合、面配送の拠点へのアクセスを考えた拠点配置を検討することとなる。
輸送の改善においては積載率の向上をいかに図るかがポイントであり、面配送の拠点へのアクセスを含む幹線輸送の積載率確保は重要な施策となる。自社の荷量では積載率が確保できない場合には、共配体制が取りやすい立地に拠点をおくこと、および適切な運送会社パートナー選定が必要である。
調達物流については、平均化した物量をコンスタントにローコストで受け入れ可能な仕組みを考える。海外からの直貿易による調達であれば、輸入港の見直しや生産地(海外)での在庫一時保管も検討すべきである。平均化した物量をコンスタントに受け入れるメリットとしては受け入れ作業の平準化・在庫スペースの圧縮などの効果が期待できる。
(2)作業の改善
作業面の改善について最も重要なことは「ムダどり」である。
ムダどりが重要なのは、物流現場では手待ちのムダがもっとも多いからである。代表的な例として、ピッキングと検品の工程を分けている場合はどうしてもピッキングが追いつかず検品が手待ちになる、もしくは検品が追いつかず検品待ち商品であふれるといった状態になりがちである。もちろんそのような状況を見てピッキングと検品の人数調整を行うが、人数調整が必要と判断した時点では、すでにムダが発生しているということに気づく必要がある。PCP出庫方式(※)など、業務フローの変更でムダ自体が発生しない仕組みに改善することが肝要である。
※ピッキング・チェック・パッキングの略で、一人の作業者がピッキングから検品・梱包までを担う方式である。
次に重要なのは「業務の平準化」である。
平準化については、大ロット作業の方が効率が良いように見えるが、人数調整が難しく、手待ちが発生しがちである。また、荷捌きペースもその時だけ必要となり結果的に効率が良いとは言えない。水がスムーズに流れるように一定の量を常にコンスタントに処理することが、効率の良い作業を行うことにつながる。平準化を意識した作業方法を検討することと合わせて、販売の末端が365日の営業を行っている中で、平準化を考えれば当然土日を含めた倉庫稼働も検討すべきテーマとなる。拠点立地の観点からは人員調達面での土日稼働の容易性を検討することが必要である。
(3)保管の改善
保管面での改善については、在庫削減が最重要テーマである。
販売数に合わせた在庫量を持つことは物流のみならず企業運営の基本であり、現在のように顧客の消費動向が縮小かつ変化が激しい時には、ロット生産によるコストダウン効果は不動在庫になるリスクを超えられないと考えるべきである。
調達数量の適切化にめどを付けた上で、DC拠点のTC化・TC拠点の新設・必要面積の精査・坪当たり単価を検討し、拠点政策に反映させることが望ましい。
海外からの直貿易による調達であれば(輸送の部分で記載したように)、海外での在庫保管も検討すべきである。ジャストインタイムの入荷が可能になれば保管面積の削減が可能となる。かつ国内の物流センターを経由しない「海外から顧客(最終目的地)への直送」を実現できれば更なる削減が見えてくる。例えばアパレル業界では(季節変りの)商品入替時の大量出荷と売れた分を補充出荷する作業があるが、大量出荷分については物流センターを経由せず直接納品先に送付することで物流センターのスペース圧縮に取り組む事例が増えてきている。
拠点のあり方については、昨今の震災の経験から、上記の判断基準以外にもBCPの視点も考慮することが求められる場合もある。拠点の分散・集約については各社の方針に乗っ取った判断を行うことになるが、拠点分散による在庫数増加に関しては、通常時の拠点機能と緊急時の拠点機能を分けて考えることを検討したい。
まとめ
以上、改善の必要性と輸送・作業・保管の各観点からの改善方法の一例についてまとめた。改善の設計は物流会社主体ではなく荷主企業が主体的に行うことが肝要である。
今後、単価ダウンによるコストダウンが難しくなる中で、本格的な改革・改善によるコストダウンに取り組んでいただくきっかけとなれば幸いである。
おすすめ情報
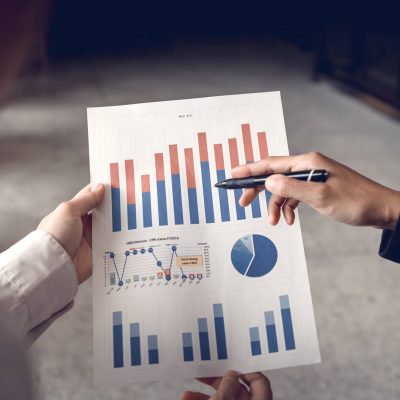
〔サービス〕物流コスト削減
- 概要
- 企業経営におけるコスト削減は終わりのない要求であり、各社いずれの企業も永続的な取り組みを実行しています。
物流に関わるコスト(輸送費・荷役費・拠点費・返品費・情報システム費等)を総点検し、市場価格とのギャップを抽出。実行に必要な改善具体施策を策定いたします。 - 詳細
- https://www.f-logi.com/ninushi/service/cost-reduction/